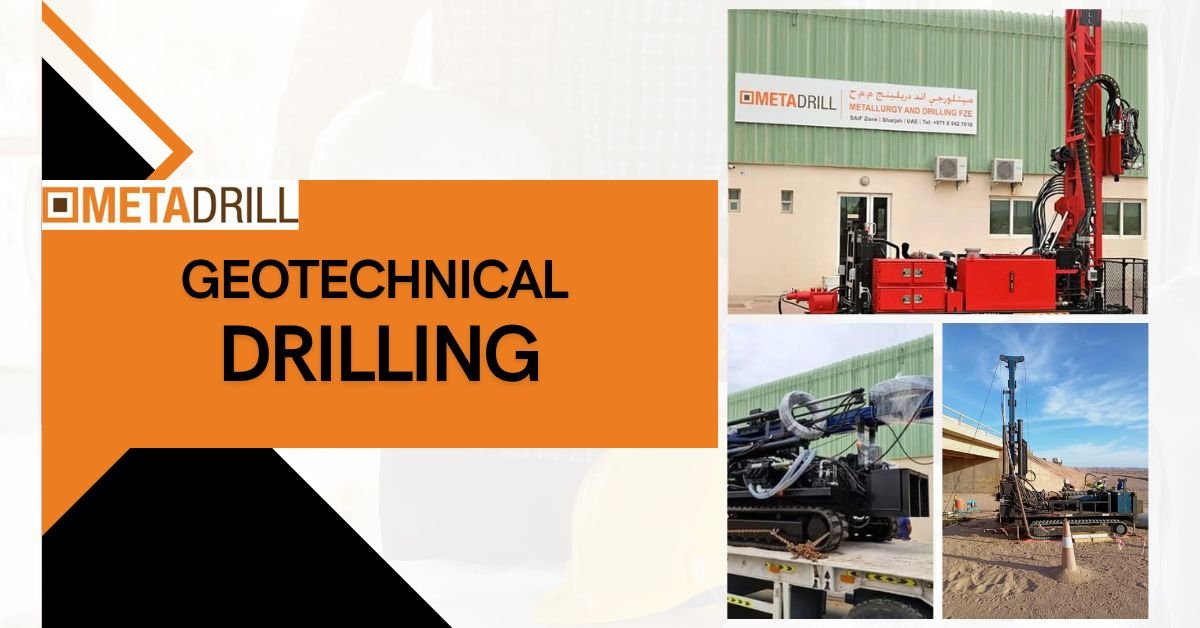
It is indispensable in construction and environmental projects, providing valuable data on the soils, rocks, and groundwater. However, it does come with many serious challenges that thwart projects in terms of timeliness, budgets, and even safety. This article describes the five leading challenges facing geotechnical drilling, explores some innovative ways that geotechnical drilling companieshave set up to surmount such challenges, and points out why selecting the correct geotechnical drilling company is essential for one's project. In this effort at better appreciation for the complexity involved in geotechnical drilling and the importance of planning and execution, these challenges and their solutions will be further discussed.
Challenges and Solutions in Geotechnical Drilling
Geotechnical drilling is indispensable in construction and environmental projects. The process provides important data regarding soil and rock conditions and even those related to groundwater. However, this process does not come without challenges. Here are the top five challenges in geotechnical drilling and how companies address these challenges:
- Site Accessibility and Difficult Terrain
Challenge: One of the many challenges within the geotechnical drilling industry is access to remote or inaccessible sites. Rough terrain, steep slopes, and heavy vegetation may impede heavy machinery and personnel motions used in drilling.
Solution: The companies get special equipment for rough terrain, including all-terrain vehicles, usually ATVs, and portable drilling rigs. Such rigs are lightweight and can thus easily be transported to a remote site. Companies may even charter helicopters to airlift the equipment to incredibly inaccessible sites. In addition, proper planning with site surveys is a prerequisite to identifying the best access routes and ensuring minimum environmental damage. - Subsurface Conditions and Unexpected Obstacles
Challenge: Significant variations in subsurface conditions concerning soil types, rock formations, and underground utilities often pose a considerable challenge. The consequences may include damage to equipment and increased costs due to unexpected delays.
Solution: Accurate and detailed geophysical surveys before drilling can establish the most favorable subsurface conditions and obstacles. Several methods, such as GPR and seismic surveys, provide much information on the subsurface. Moreover, companies utilize adaptive drilling techniques, such as rotary and sonic drilling, to work with different soil and rock types. Continuous real-time monitoring and analysis during drilling also allow immediate adjustments to the drilling plan. - Groundwater and Environmental Considerations
Challenge: Groundwater complicates the drilling process by destabilizing the borehole and malfunctioning equipment. Other possible environmental dangers drilling poses include contamination of groundwater and disturbance of natural habitats.
Solution: To manage groundwater issues, companies use drilling fluids and mud to stabilize the borehole and avoid collapse. Other dewatering techniques entail pumping and wellpoint systems to control groundwater levels. Measures protect the environment through biodegradable drilling fluids and appropriate waste disposal. EIAs are also conducted to identify and mitigate potential risks. - Reliability of Equipment and Maintenance
Challenge: The challenge is that the drilling equipment must work in harsh conditions. As a result, wear and tear, breakdowns, and increasing maintenance difficulty will result. Equipment failure results in huge delays and raises project costs.
Solution: Preventive maintenance and regular monitoring of the drilling equipment are especially important in ensuring its reliability and durability. Most firms thus engage in routine preventive maintenance programs involving checks, lubrication, and replacement of worn-out parts. Investment in durable capital equipment and personnel training in the best practices of operation and maintenance reduce the frequency and duration of failures. Delays can be further reduced by having standby equipment and spare parts at the site to handle unexpected breakdowns. - Data Accuracy and Interpretation
Challenge: The challenge is that data collection and interpretation in geotechnical projects may be considered problematic. Any defects or incompleteness in the data lead to design errors, safety issues, and increased costs.
Solution: The firms implement advanced data collection equipment, such as CPT, SPT, and geotechnical software, for accurate data gathering. Drilling personnel should be well-trained and experienced in data interpretation and collection. Data quality control allows for better accuracy through the cross-checking of results using various data sources. Collaboration with geotechnical engineers and experts ensures the data is correctly interpreted and applied to project designs.
Final Thoughts
Geotechnical drilling forms the foundation for many construction and environmental projects. However, it can also be incredibly challenging. Learning about common mistakes and unique solutions employed by geotechnical drilling companies helps project teams prepare for issues and limit potential risks.
Operating countrywide, MetaDrill is one of the most significant geotechnical drilling companies with a well-established history of addressing these issues to provide safe, accurate data. Combining specialist expertise with state-of-the-art equipment and concern for environmental sustainability, MetaDrill will become the partner that will allow any project requiring geotechnical investigations to be performed.
This would mean project teams can have informed, supported projects with accurate, reliable data as an outcome of engaging a reputable geotechnical drilling company like MetaDrill.
Question to the public: